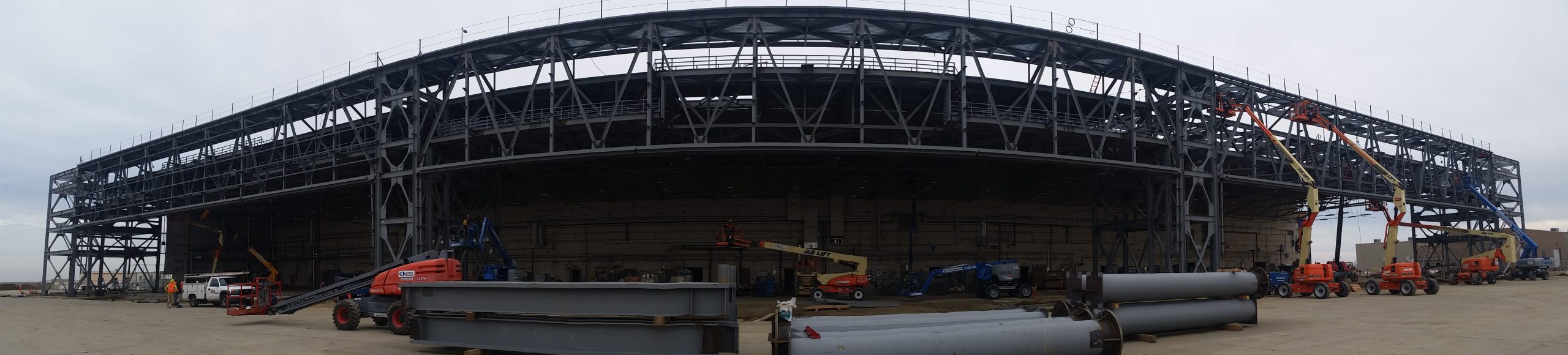
Frequently Asked Questions
Welcome to our Frequently Asked Questions (FAQs) page. Below you will find info on:
- Projects
- Safety
- Service
If you have a question that isn’t answered here, pleaseĀ contact us.
How long has Triad Steel Service been in business?
Triad was founded in 1995.
What certifications and licenses does Triad possess?
We’re an AISC certified fabricator and we’re approved by the City of Los Angeles, City of Phoenix, and Clark County, NV We are currently licensed in Arizona, California, and Nevada.
Does Triad erect the steel it fabricates?
Our scope of work typically includes both fabrication and erection. We work with our highly qualified Erector partners to erect our fabricated steel on each project.
Does Triad utilize union or non-union labor?
We employ non-union workers in our shop. In the field, we utilize and work equally well with our union and non-union Erector partners.
Is Triad involved in the BIM concept of project design and execution?
From a steel fabricator’s perspective, we consider ourselves on the leading edge of BIM development. Our detailing software produces LOD400 (and near project completion, LD500) 3D models exports and we are not shy to participate in pre-construction coordination and clash detection efforts during each project if requested.
What’s Triad’s philosophy towards safety?
Simply stated, safety is top priority both in our shop and at our job sites. In our shop, we have a comprehensive training program to keep our employees working safely. In our office, the majority of office personnel are OSHA 30 certified in the event they need to go to a jobsite. In the field, our Erector partners are fully trained in safety, accident avoidance, and OSHA Sub-Part R (steel erection) to be safety conscious while always complying with our customer’s safety rules while on site.
Why would I want Triad on my project?
As our company name says, we are service driven. You won’t find a more proactive, professional, problem avoiding, “team player” steel subcontractor.
What’s Triad’s philosophy towards problem resolution?
One of our primary goals is actually problem avoidance. We’re forward-thinking in that we thoroughly plan each project so potential problems are identified and resolved as quickly as possible. Should a problem arise, we participate in discussions with our customers and the design teams, analyze the situation, and recommend the most economical solution(s).
Does Triad have any special capabilities that aren’t typically provided by other steel fabricators?
Triad excels on complex projects with tight schedules – projects that require significant project management effort and coordination with our customer and the design team.
How does Triad staff each project?
Basically, whatever it takes to meet the project and our customer’s needs. More specifically, on larger projects we’ll have a project management team consisting of one to three people if project size and complexity requires it. On all projects, our management teams are no stranger to the jobsite.
What is Triad’s view on the importance of project management?
Executing three key components (scope, schedule and budgets). Provide a quality product, be the least of your problems, do what we say we’re going to do, be proactive and propose solutions to problems.
What steps does Triad do to insure that a schedule is met or improved?
We track and monitor our project schedules and commitments by using one of several scheduling software programs. If our customer comes to us looking to improve upon a previously determined schedule, our company has always encouraged employees to think “outside of the box” in brainstorming sessions that very often lead to great alternative options and results for our customers.
How does Triad solve problems in the field?
Our Project Managers are easily accessible and in no stranger to job sites and make frequent visits. Quick communications and a strong field presence are a must for solving problems in a timely manner.
Are there any advantages or disadvantages between a bolted and a welded connections?
We prefer bolted connections in most cases, specifically for field conditions. It can be more cost effective to bolt in lieu of welding in most cases.
Detailing is a very small percentage of the steel contract. How important is it to the overall success of a project?
Although detailing is a small percentage of our costs on each project, we know that good detailing is the critically important starting point to a successful project. It’s definitely not an area to cut corners to save money. We carefully evaluate and select detailers who provide accurate and complete shop drawings within our project schedules.